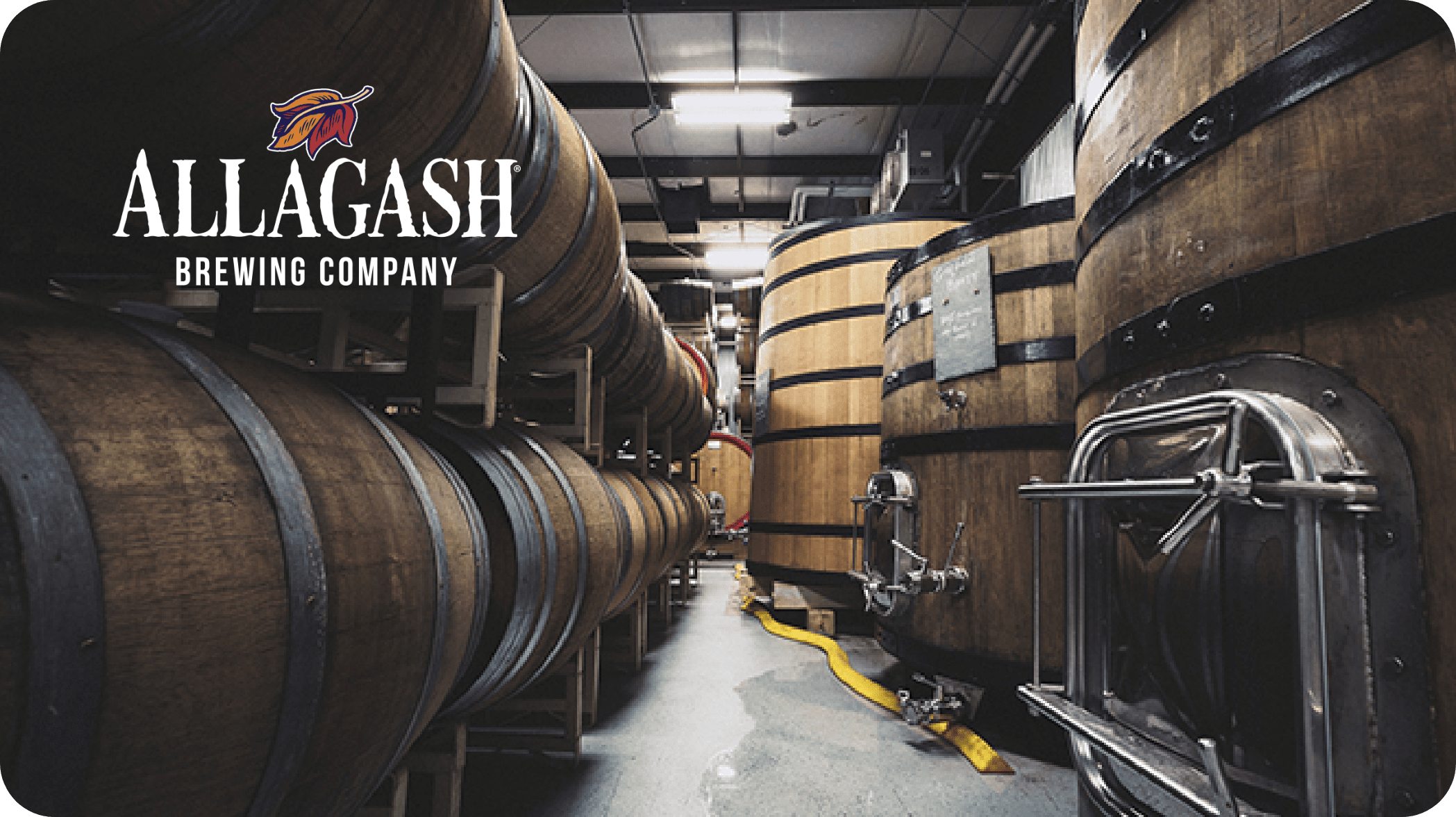
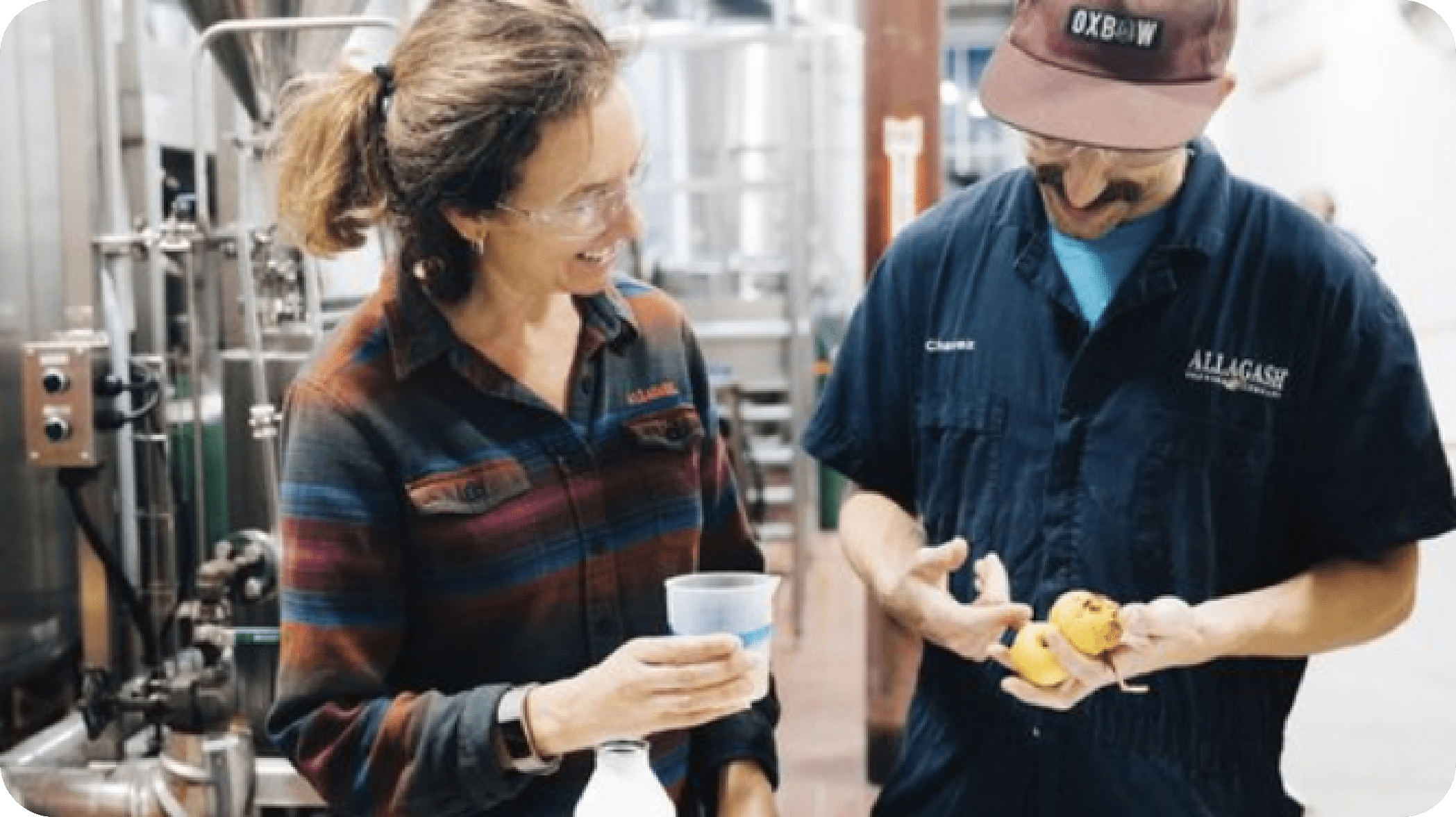
For the past three decades, Allagash Brewing Company – which today is one of the largest craft breweries in the United States – has been at the forefront of the craft beer movement, brewing up some seriously delicious and creative beers out of their Portland, Maine brewery.
In their ongoing efforts to improve the efficiency of their system and the quality of their products, the brewing team at Allagash had a pre-heating wort skid installed in their brewery – an important investment that, when in full operation, can save them up to 20 minutes per brew cycle.
However, once installed, the Allagash team struggled to commission the wort skid into their system: they encountered issues getting the skid up to the right temperatures, and, in addition, the skid was emitting noise levels in excess of 100 DECIBELS – which is not even safe to be around, let alone endure while trying to enjoy a cold, refreshing Allagash White Ale.A Need for Speed
As every process engineer understands all too well, not being able to quickly and efficiently dial in an expensive piece of equipment once it is installed can put you in an extremely difficult (and costly) situation. And the longer it takes to fully commission the equipment into your system, the greater the negative impact on the return on investment.
The brewing team at Allagash needed to resolve these issues, and they needed to resolve them quickly.
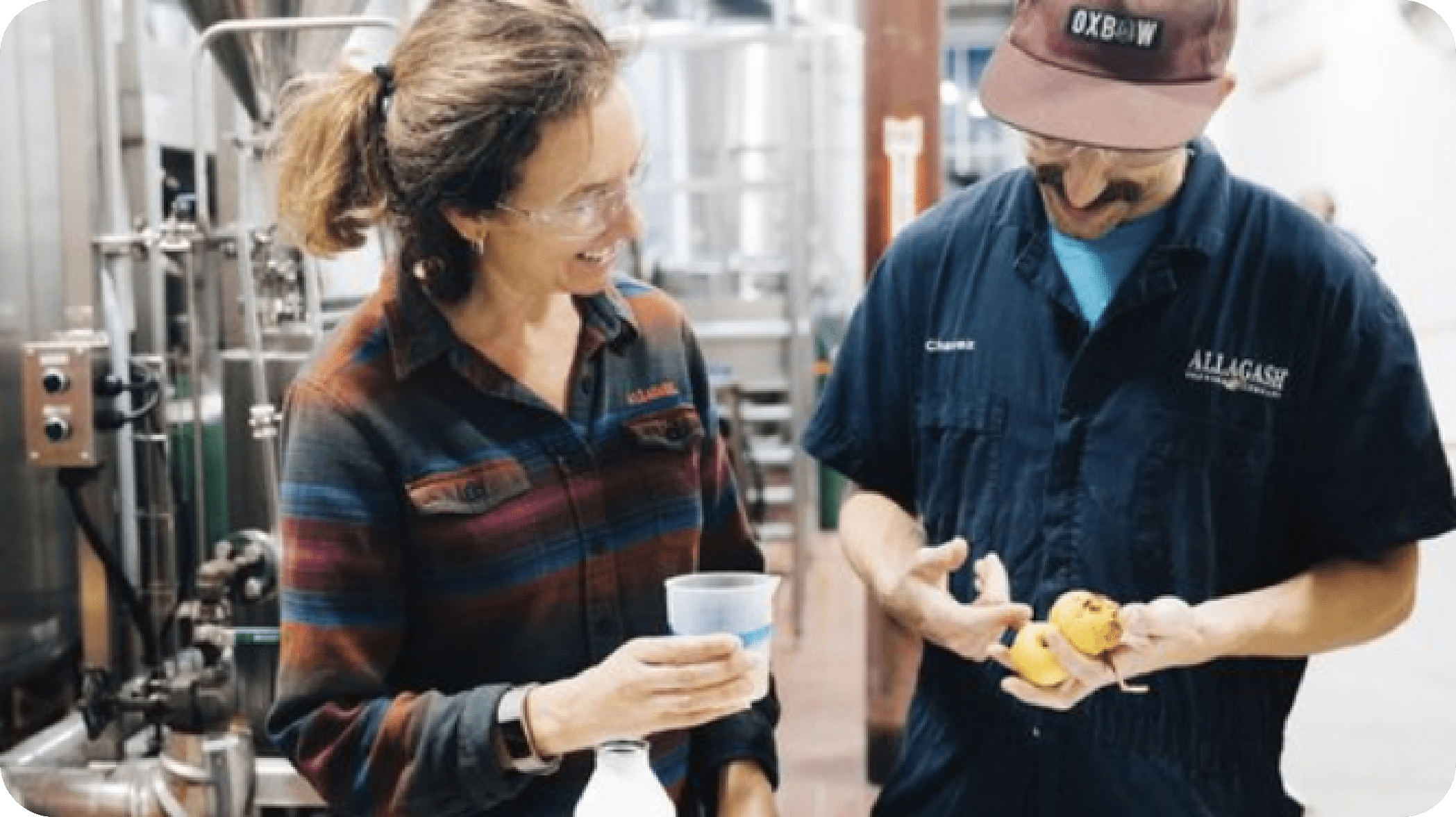
What to Do?
The Allagash brewing team needed a way to collect data so the wort skid manufacturer could help them troubleshoot the process. Specifically, the team needed to obtain extremely accurate temperature measurements at very specific locations within their system, where there were no existing sensor ports.
But how? What are the options for fast, accurate, specifically targeted temperature measurement?
Well, for one, the brewing team could install traditional invasive immersion sensors into these specific locations within their system. But this would be an expensive, time-consuming (and did we mention expensive?) process. Allagash would have to purchase the sensors, hire a sanitary welder, shut down their process, and install the sensors – all for a single, one-time temperature measurement. Accurate, yes. But neither a time-saver nor a cost-saver.
Another option is surface sensors, which attach directly to the outside of the pipe. The problem with using these types of sensors is that while accurate, they measure the wrong thing! Since these sensors measure the temperature of the outside of the pipe and not of what’s flowing inside – which is what is needed – they would not provide valuable information for this situation.
A third option would be to use infrared (IR) thermometers to spot-check temperatures at these specific locations along the stainless-steel pipes of the brewing system. However, when IR thermometers are used on stainless-steel pipes, they become unreliable and are often not very accurate. Since high accuracy is a necessity for Allagash in this situation, IR thermometers are out.
So, as you can see, no option is exactly ideal.
But now, thanks to innovative new technologies developed by Omega engineers, there is another option. An ideal option: the HANI option.
The HANI Sensor
Omega’s HANI High Accuracy, Non-Invasive Clamp Temperature Sensor clamps right onto the outside of a desired pipe and measures the fluid inside with as much accuracy and with the same high performance as traditional invasive sensors – but without any of the installation headaches, contamination risks, maintenance costs, or production shutdowns.
It’s quick, it’s cost-effective, and it’s highly accurate.
From unboxing to measurement-ready, HANI sensors take about 10 seconds to install. Just wrap the sensor around the pipe in the desired location and clamp the quick-latch mechanism (one of our other brewery customers described it as “literally the easiest thing I’ve ever done”). There’s no need to cut, weld, drill, or shut down production to install or move a HANI sensor. And, once mounted, you can start logging highly accurate, immersion-probe-level temperature measurements.
With a single HANI sensor, and its flexibility (it can attach literally anywhere the team wants along a pipe within their system), the Allagash brewing team began to do some testing.
First, they initiated a brew cycle without running the wort skid. During this run, the brew team was able to take measurements at a very specific location within their system using a well-placed HANI sensor where they otherwise would not have been able to place a temperature sensor. With these measurements, the brew team proved their process could achieve the required temperatures.
As a second test, they ran the brew cycle with the new wort skid in operation. Since HANI sensors are so easy to reposition, the team was able to quickly take measurements at different points in the process to show where the required temperatures were not being met.
The data collected from the HANI sensor gave the brewing team essential information that they were then able to provide to the manufacturer, and in turn, assist Allagash in getting the wort skid integrated into their system.
Ultimately, the versatility, the non-invasiveness, and high accuracy of the HANI sensor helped Allagash expedite the commissioning process of the wort skid – enabling the skid to be deployed, delivering their ROI, and eliminating unnecessary downtime due to faster troubleshooting.
More About HANI
Developed with the objective of providing a better, more efficient, and more cost-effective alternative to the status quo method for accurately measuring the temperature of fluid media inside of a pipe – which is to use an invasive immersion probe – the HANI Clamp Temperature Sensor is a complete game-changer for not only professionals in the craft beer brewing industry, but for any process or system that requires high accuracy, fast response times, and easy installation.
The HANI mounts like a surface sensor but performs like an invasive sensor. With HANI sensors:
- No cuts or welding needed
- No downtime or production halts
- Install in < 30 seconds
- Immersion probe level accuracy